Surface preparation is a very important step towards achieving a visually clean surface and satisfactory surface profile. Surface preparation is done before applying any type of coating or paint on the surface of metal, glass, concrete, or wood. Skipping this step leads to many problems for instance flaking of paint, corrosion of metal substrates, and the production of rust. Thus, surface preparation is a crucial part of achieving a clean profiled surface. How is the surface preparation achieved? It is done through a process called abrasive blasting or sandblasting.
What is abrasive blasting?
Abrasive blasting is a loose abrasive machining process. In this procedure, compressed air is used to direct abrasive media towards the workpiece or surface at high speeds. There is also another way of doing it which is through centrifugal force induced by a spinning wheel. Like this, excessive or unwanted materials are removed from the surface so that they don’t adhere to the new coating.
The first abrasive blasting technique was introduced by Benjamin Chew Tilghman in 1870. He observed it from nature’s technique of using high-speed flowing water to prepare the surface or wind-blown sand. Through this observation, he planned to introduce abrasive blasting in which the abrasive media used was sand. But later on, this abrasive media and this type of abrasive blasting was stopped as the sand (silica) caused silicosis, a respiratory disease that was dangerous for both the workers and the surrounding environment.
What is the purpose of abrasive blasting?
The intention of using the abrasive blasting process is to remove contamination, corrosion, and any type of damaged coating to prepare a new surface. Other names for abrasive blasting are sandblasting grit blasting, and media blasting. The common uses of the abrasive blasting process are:
- Making a rough surface smoother
- Making a smooth surface rougher
- Profile a surface
- Removing surface contaminants such as paint, rust, or residues
- Cleaning and preparing a surface before any further application: making the surface workable to improve the adhesion of new coatings.
- Finishing a surface: this means that this process can be used to create decoration on the surface too.
You can achieve the desired surface by using the particular abrasive media in the abrasive blasting process. There are several types of abrasive media, each specific to its use. What are they?
- Steel shot (shot blasting)
- Steel grit
- Glass beads (bead blasting)
- Aluminum oxide
- Crushed glass
- Garnet
- Silicon carbide
- Sodium bicarbonate
- Plastic grit
- Coal slag
- Pumice
- Copper slag
- Cut wire
- Ceramic grit
- Walnut shells
- Corn cobs
- Apricot, peach, or plum stone powder
- Dry ice
These abrasive blasting media have their specific properties upon which they are chosen for the particular kind of task. All of them have different densities, hardness, shapes, and particle sizes.
How this blasting process works?
The blasting machine consists of three main parts: an abrasive container or blasting pot, a propelling device or mechanism, and a blasting nozzle.
The media is propelled at high velocities or by centrifugally-powered wheel force to the surface. The media can be recycled until it is all finished in a blasting cabinet, blast room, or shot blaster. In outdoor blasting, it needs to be analyzed whether the abrasive media can be recycled or must be disposed of.
There are two types of mechanisms of abrasive blasting:
- Dry blasting:
Dry blasting is used to affect the surface by using propelled air to project the abrasive media onto the surface. In other words, it is used to give texture to the surface.
- Wet blasting:
Wet blasting is used to project a stream of high-pressure water to clean the surface.
Both of these mechanisms are used to give a more tuned and finished profile to a surface. Wet blasting is comparatively more ideal to use as it does not leave residues behind and you don’t have to spend time cleaning at the end. Whereas, dry blasting requires a dust collector that is used to collect the dust and filter it from the blasted surface and spent media.
What are the types of abrasive blasting?
There are various types of abrasive blasting; each has a different purpose according to the choice of surface preparation.
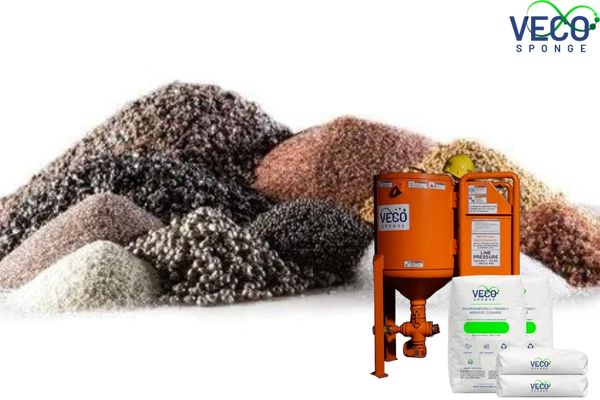
- Bead blasting:
In this type of blasting, glass beads are used at relatively low pressure. They are used in cleaning, deburring, and peening of metal surfaces. They are used in removing paint, rust, and corrosion from metal surfaces. The smaller the glass beads, the smoother the surface. They leave a dimpled texture on the surface afterward. They can be used in both dry and wet blasting. They are non-toxic and safe for both the environment and the workers.
- Shot blasting:
They are also used in the surface preparation of metals. It consists of spherical steel shots to be blasted. The peening effect is produced with shot blasting and it gives an extra strength to the blasted surface. It can take place in a blasting cabinet, in blast rooms, or in enclosures.
- Wheel blasting:
If you are using heavy abrasives such as shot or grit, then it is recommended to use wheel blasting. In this blasting, the centrifugal force of a wheel is used to propel media to the surface instead of water or air.
- Soda blasting:
In this blasting, sodium bicarbonate is used to blast surfaces with the help of compressed air as a propellant. Soda blasting is used in automotive restoration, rust removal, wood cleaning, graffiti removal, soot remediation, and cleaning of boat hulls.
- Dry-ice blasting:
Dry ice is referred to the carbon dioxide pellets that are propelled by air towards the surface. This is safe blasting and is used to blast surfaces of food processing tools.
- Micro-blasting or pencil blasting:
This type of blasting is done with specialized tools which are used to blast small surfaces. Its common use is in glass etching and detailed applications.
There is a range of purposes for abrasive blasting. It is ideal to use in a variety of industries where it gives a lot of benefits. It is mainly used in:
- Shipbuilding and hull cleaning
- Automotive repair and restoration
- Construction and contracting
- Metal Finishing
- Welding
- Metal casting and foundry work
- Surface coating or powder coating
- Painting
- Surface Preparation
- Glass work
- Concrete
- Monument engraving
- Winding up:
Analyzing all about abrasive blasting, it can be seen that this process is very helpful in achieving different and desired results due to the variety of abrasive media and its techniques. It’s a highly efficient and faster cleaning process as compared to other manual methods. It is ideal for hard-to-reach areas and tiny details that you can’t achieve through other methods. Besides being an ideal procedure, there are some safety precautions you need to consider while working with this method. Therefore, by considering the safety measures and choosing the right material you can achieve your expected results.
Leave a comment